Gas Turbines
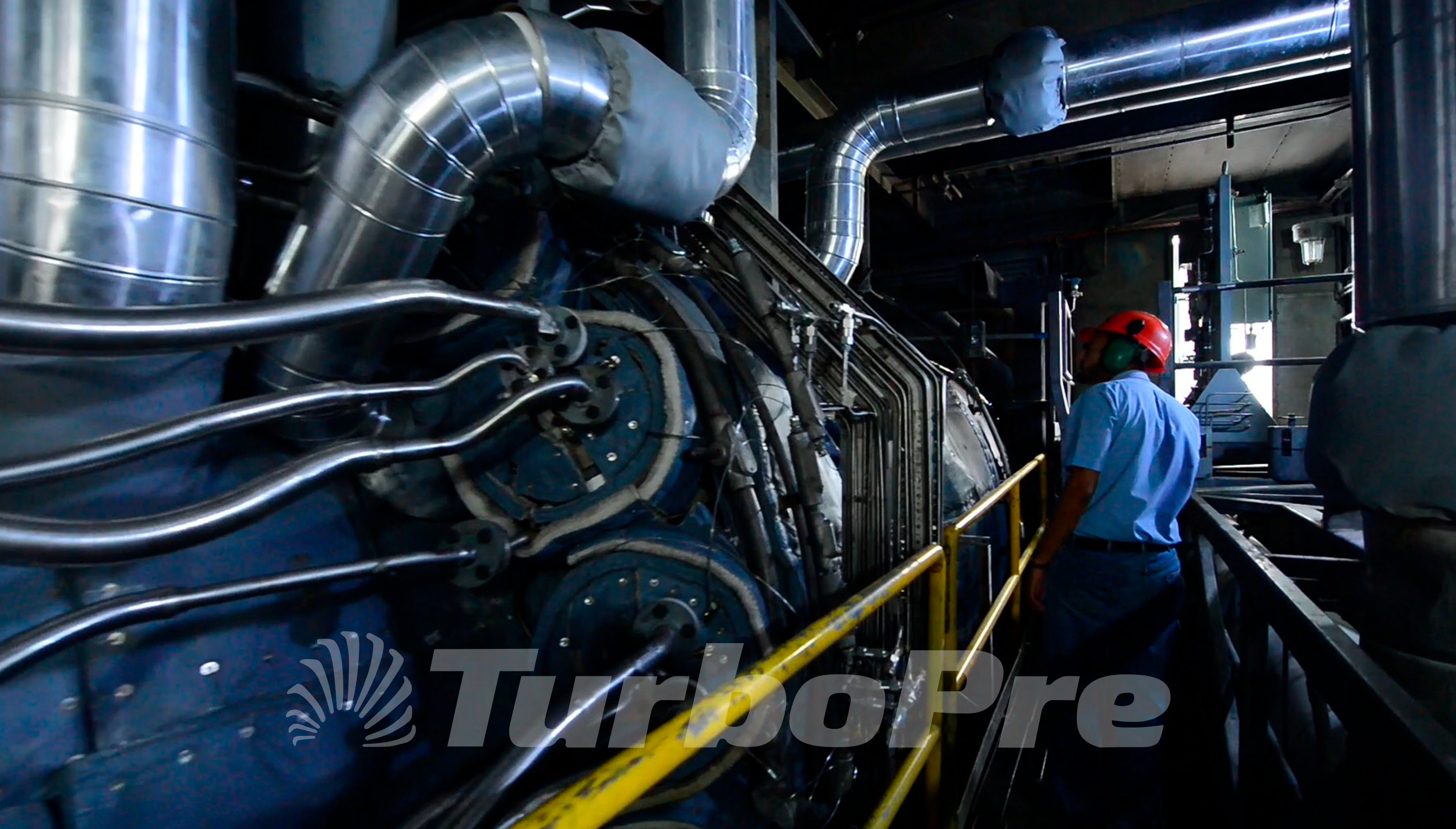
In the combustion inspection, a remote visual inspection is carried out to determine the conditions of the internal components. Based on the findings detected, the removal, inspection and replacement, if required, of pipes and the atomization and purging air system are carried out; cooling and seal system, fuel injection nozzles, combustion chamber covers, flame arrester tubes and combustor baskets. This practice varies depending on the technology of the gas turbine and the quality of the fuel used; its execution range is between 8,500 and 12,500 HH.
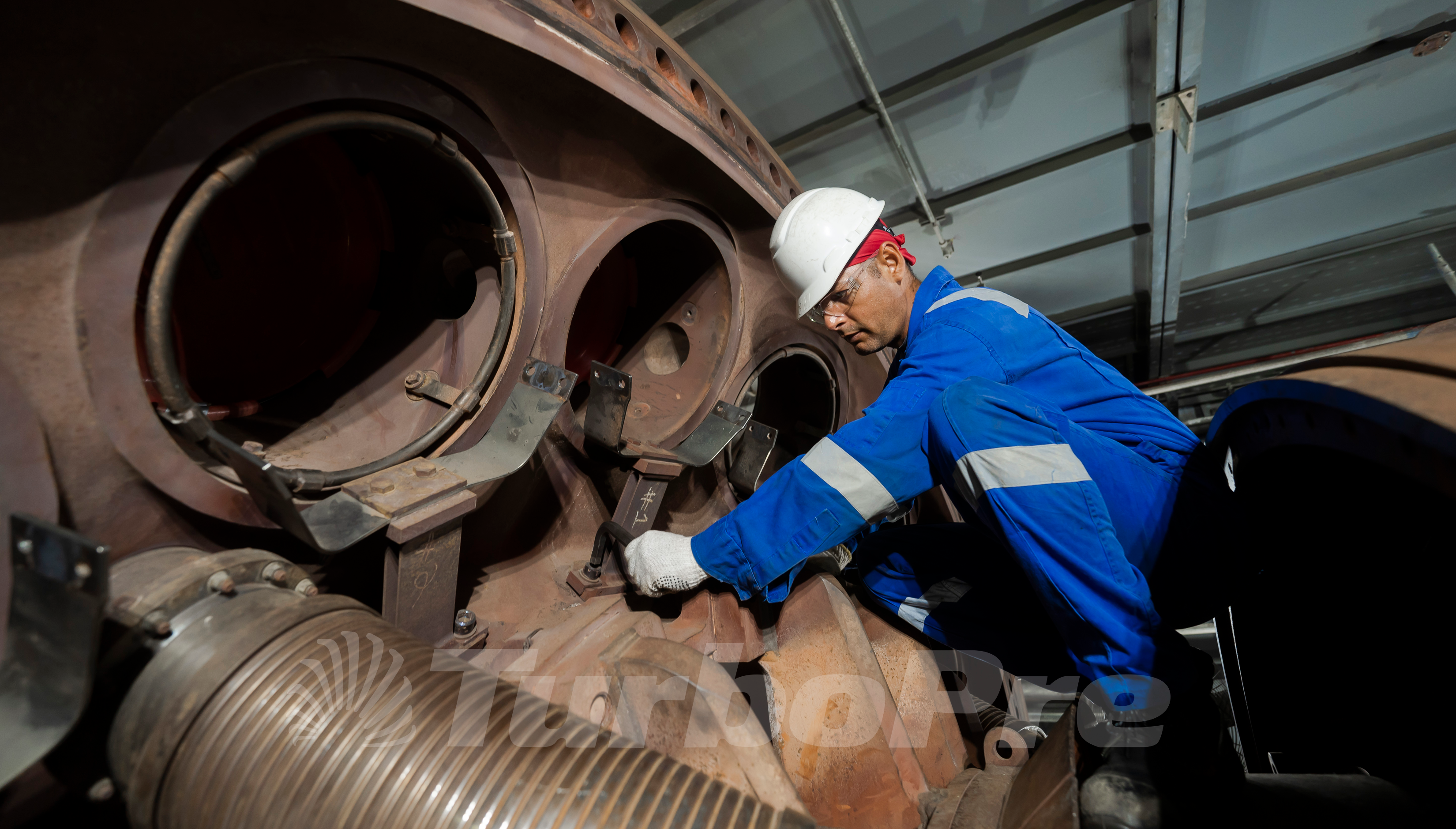
In this phase, the elements of the combustion section are usually replaced: combustor baskets, injectors, transition pieces and elements of the turbine section such as blades and nozzles in order to reestablish the conditions of the turbine for another operating cycle. This practice varies depending on the efficiency of the combustion inspections carried out, the quality of the fuel used and their execution interval is carried out at 24,000 HH.

This type of maintenance is carried out once 48 thousand hours of operation have been completed. During this phase, static and dynamic components are involved, and critical components are replaced (at the static level and the turbocharger rotor).
In addition, the inspection of the passage of hot gases and the disassembly of the unit are included. Inspection and repair of the inlet air filter and duct, diffuser and exhaust expansion joints, IGV combustion components, compressor and turbine blades, inlet chamber and exhaust plenum, inspection of load couplings and valve are also carried out made out of fuel.
Maintenance of auxiliary equipment and control system:
Parts Supply.
Component repair.
Maintenance of auxiliary equipment.